TG Escapes Blog
What Are Modern Methods of Construction?
Modern Methods of Construction (MMC) are a broad spectrum of building techniques used to create everything from temporary buildings to massive skyscrapers, focusing on off-site manufacture and prefabrication. Utilising these methods offers significant benefits to cost efficiency, project timelines, and environmental sustainability.
While these advantages have been clear for many years, permanent modular buildings are still subject to misconceptions about their quality and aesthetic appeal across the UK. TG Escapes are an award-winning producer of MMC buildings, predominantly working in the education and commercial sectors, and we’ve created this guide to showcase the potential and versatility of modular buildings in addressing today's construction needs.
What is the definition of a modern method of construction?
Modern Methods of Construction encompass an array of off-site and on-site techniques aimed at enhancing traditional building methods. Originating in the aftermath of World War II to combat the pressing need for rapid housing delivery, the elements of the building will be produced at a different location, usually in factory conditions, before being transported to the site and connected as a finished building. While portable buildings will be made from a single standalone unit, most modular buildings are constructed from many pieces.
Why do we need alternative methods of construction?
Conventional brick-and-mortar construction methods, while standardised within the UK, present a wide variety of challenges that make them increasingly untenable, especially their brutal environmental impacts. This is also true for larger buildings, which require high levels of concrete in their production. Here are some of the key issues with established construction methods:
- Wastage: Traditional construction contributes significantly to material wastage, with construction and demolition activities accounting for 32% of landfill waste, and a staggering 13% of products delivered to building sites sent directly to landfill without being used. This not only represents a substantial loss of resources but also burdens our already overflowing landfill sites.
- Environmental issues: The environmental footprint of traditional building techniques, particularly the use of materials like concrete, is profound. Concrete production is one of the largest sources of carbon dioxide emissions, making the construction industry a major player in environmental degradation. Concrete also uses huge quantities of sand, contributing to a global sand crisis.
- Quality issues: While traditional methods can deliver quality outcomes, they also present a risk of inconsistencies and defects. Issues such as dampness, thermal inefficiency, and structural defects can arise, leading to increased maintenance costs and reduced building lifespan.
- Timelines: Delays are a common setback in traditional construction, caused by everything from weather issues to poor planning and resource management. These delays can significantly impact project timelines, leading to increased costs and frustration for all stakeholders involved.
In the aftermath of World War II, the urgency to rebuild provided a catalyst for exploring more efficient construction methods. Today, factors around speed and price are still important, but sustainability is the more crucial selling point for MMC, with them routinely discussed as the best way to create net zero buildings.
What types of MMC are used in the UK?
Various types of buildings and techniques fall under the MMC umbrella. When looking to design and build off-site before installing on-site, companies can create everything from portable buildings, which are delivered as a single finished unit, to the bespoke panellised designs our team create, which are assembled as finished buildings on-site.
Panellised systems
Panellised construction systems involve the assembly of pre-made flat panel units (such as walls, floors, and roofs) in a factory setting, which will then be transported to the construction site for quick assembly. These can be designed as open or closed panels, with closed versions often arriving on-site with windows, doors, and even external finishes pre-installed. This method significantly reduces build times and minimises waste, making it an attractive choice for projects looking to balance efficiency with environmental considerations.
The panellised modular approach also offers a great deal of architectural flexibility externally and internally, allowing varied room shapes and sizes, and attractive designs. Our team utilise a panellised modular approach, building timber panelling at our off-site manufacturing facility, and installing them around our durable timber frames. For our designers, it offers a great level of customisation and visual style while maintaining our high sustainability goals.
Volumetric systems
Volumetric construction involves creating fully equipped three-dimensional units within a factory, which are then brought to the site and stacked to form complete structures, from houses to flats. Utilising materials like steel and timber, volumetric construction is an efficient method for producing multiple identical units, speeding up work, ensuring uniform quality and reducing on-site work.
Hybrid systems
Some producers of MMC buildings utilise both panellised and volumetric elements within the same building, for instance installing a volumetric kitchen or bathroom within a more bespoke panellised house.
MMC Components
There is also a range of prefabricated components that can be incorporated into an MMC building, from foundation systems to floors to roofs, alongside plumbing and wiring. All of these elements offer the performance and quality expected from a traditional building in a greatly reduced timescale.
The advantages and disadvantages of MMC
Modern methods of construction offer a fantastic approach to creating a building, with a range of benefits across quality, speed, price, and sustainability. While there are still changes that need to happen in terms of awareness and experience both in and outside of the construction industry, these techniques are here to stay, with the UK government making a firm commitment to utilising new technologies across their projects. There are some key benefits and drawbacks of MMC buildings to keep in mind.
Fantastic levels of quality
The quality of MMC buildings can be significantly enhanced by the precision of their factory manufacture, with every element accurately produced to match design specifications. This ensures consistency and reduces errors, leading to modular buildings that fit together flawlessly. Engineered for durability, MMC components offer long-term performance, elevating construction standards and sustainability. A permanent modular building can offer the same level of quality you’d expect from a masonry solution, with a manufacturing and installation process that ensures closer alignment with architectural plans.
True flexibility in design
Especially when using a panellised approach, modular buildings afford an extensive level of customisation. By working with a design and build company like TG Escapes, buildings can be fully tailored to meet specific needs. For our buildings, this means a huge range of sizes, room types, and layouts, with a bespoke design for each client built around their needs and locations. This method not only accommodates unique architectural requirements but also ensures that the final structure is an attractive, high-performance building.
Significant time savings
The predictable factory-based production of modular buildings significantly reduces the impact of common construction delays, such as adverse weather conditions and labour disruptions. Coupled with the swift installation process on site, MMC buildings can be completed 20 to 50 per cent faster than traditional brick-and-mortar options. This efficiency in both production and assembly phases offers substantial time savings over masonry buildings.
Consistent price reductions
Thanks to their streamlined production, reduced labour costs, and minimised waste, modular buildings typically cost up to 20 per cent less than traditional construction options. This cost-effectiveness, combined with the efficiency of the building process, makes modular construction an excellent choice for budget-conscious projects.
Environmental and sustainability commitments
Modular methods of construction offer clear sustainability benefits, simplifying the use of eco-friendly materials like timber and making the specification to net zero standards more straightforward. The controlled environment of factory manufacturing also significantly reduces material waste, as materials are precisely measured and utilised efficiently. Our timber-based, fabric-first modular approach is one of the key reasons we’re able to specify net-zero in operation as standard.
Industry inexperience
While modular construction presents numerous advantages, it also faces certain drawbacks, notably stemming from relative inexperience within the industry. Additionally, concerns arise regarding traditional building projects' ability to engage the community by providing local jobs, an aspect less prominent in modular construction due to its factory-based production, alongside a reliance on imported materials compared to UK-made clay bricks.
In the UK, there are lingering memories for many of low-quality, temporary portable buildings, which contribute to preconceptions about Modern Methods of Construction. These historical associations with inferior quality can overshadow the significant advancements and benefits that current modular techniques offer, including sustainability, efficiency, and overall improved construction quality.
Dispelling the stigma around prefabricated buildings in the UK
Today's prefabricated buildings are permanent, high-quality structures that meet all expected standards, offering a suite of additional benefits. With advancements in Modern Methods of Construction, these buildings now represent the forefront of sustainable and efficient design. Versatile across a broad spectrum of projects, these contemporary solutions deliver exceptional quality, contrasting historic associations of off-site construction.
Amazing examples of MMC building projects
As Modern Methods of Construction encompass a broad selection of methods, the types of buildings produced with them vary dramatically. Here are just 3 of the many stellar examples of MMC buildings across the UK.
- 101 George Street, London: The world's tallest modular tower is located in Croyden, a 44-storey building of 135m in height, housing hundreds of new rental units. Each floor was built from 38 volumetric modules, which arrived 95% complete, with around a week's work per floor connecting modules, services, and flooring.
- Avenue South, Singapore: These twin towers stand 56 stories tall, with around 80% of each housing module completed off-site, before being delivered and joined together.
- A ten-storey building in a day: Chinese company Broad Group has a video showcasing how their team utilise offsite manufacture and quick on-site installation to fully erect a tower block within a day.
How we create award-winning schools with modern methods of construction
TG Escapes harnesses Modern Methods of Construction to create award-winning schools that are sustainable, efficient, and tailor-made. Offering a turnkey service, we ensure projects are seamless and stress-free across design and build. Our buildings are designed to be net-zero in operations as standard, constructed from sustainable timber for an eco-friendly footprint. Every project is bespoke, meeting the unique needs of each educational community.
Speak to a member of our team today to find out more.
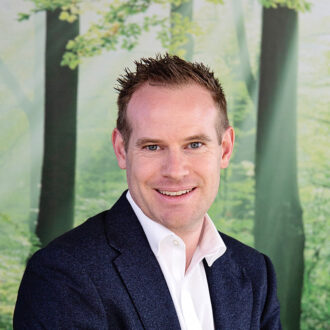
About the author
More posts from our blog
The Benefits of Choosing a Modular Clubhouse Building
A clubhouse needs to serve many functions, from creating social spaces and meeting areas to offering changing rooms and toilet facilities for players. Modular buildings are an ideal solution for creating flexible, purpose-built facilities for sports teams, schools,...
Community Buildings FAQ: Types, Uses, and Funding
Community buildings serve a wide variety of purposes across the UK, often meeting multiple needs at once. From youth centres and village halls to wellbeing hubs and community cafés, these spaces bring people together, support essential services and strengthen local...
Supporting Active School Life With Modular Sports Pavilions
Physical activity is a crucial part of everyday schooling across the UK. But in many settings, ageing facilities and limited space can prevent pupils from getting the full benefit of PE, sport, and outdoor recreation. Modern sports and leisure pavilions offer an...