TG Escapes Blog
21 Years 21 Stories: Starting In-House Manufacturing
2018 – TG Escapes Begins In-House Production
While we’ve always overseen every aspect of our design and build process, it wasn’t until 2018 that we opened our own production facility at our Coventry headquarters. We’ve been thrilled by the impact, showcased in the increasing ambition of our award-winning buildings. It’s also allowed us to store materials, which helped us manage around cost and supply issues over the tumultuous COVID years.
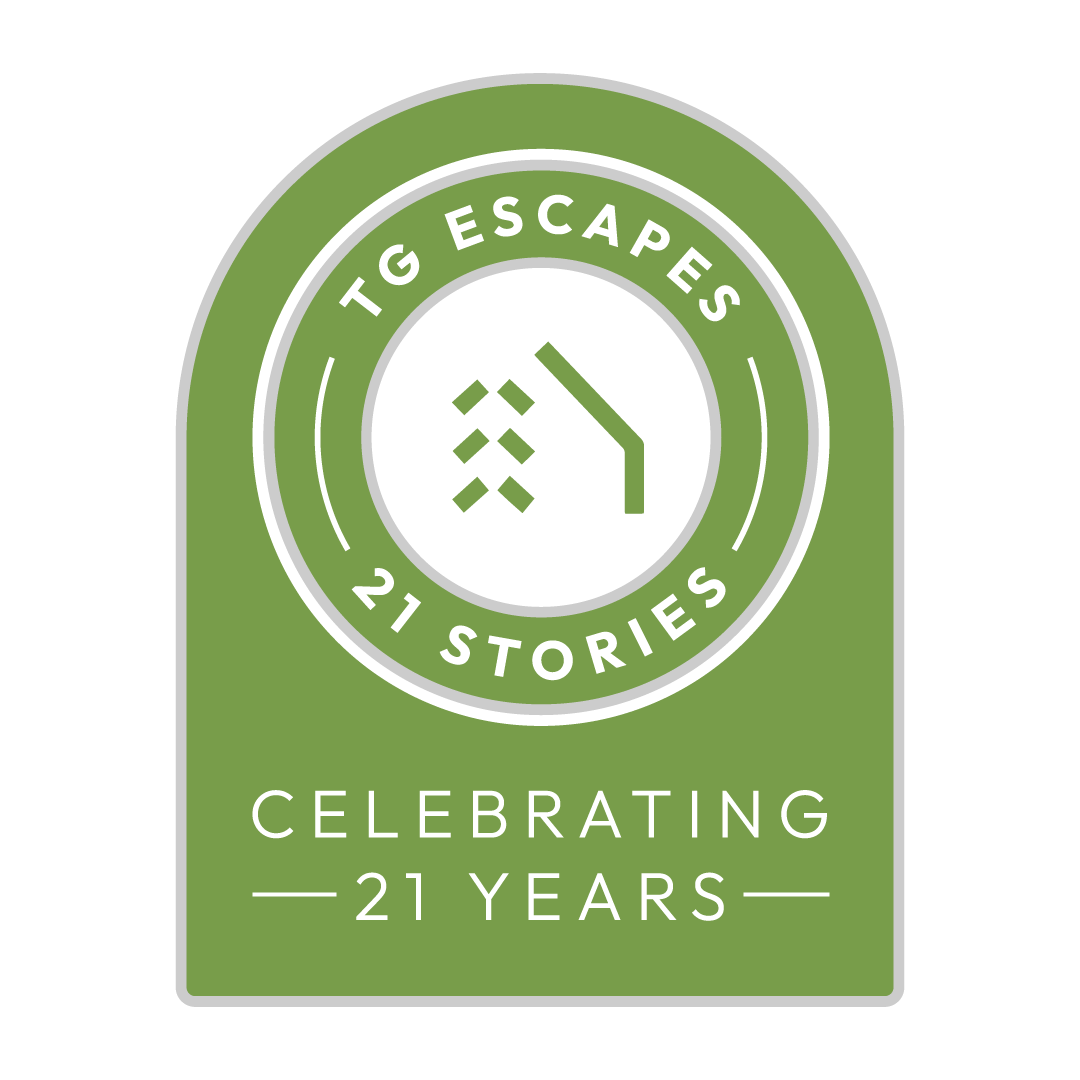
While we’ve always designed our buildings in-house, for our first 15 years the timber panels used to construct our projects were produced in Romania. In 2018 we decided to move all production to our Coventry HQ, determined to better our offerings to clients and improve synergy across the company. It gave us more control over what we were making, while also making our team far more responsive, with changes and requests communicated face to face.
Another huge benefit came from expanding our facilities by purchasing the neighbouring building. This allowed us to properly stockpile materials for the first time, which had two enormous benefits. Firstly, it allowed us to bulk buy materials, which can lessen the impact of price shifts on both us and our clients. Secondly, it allowed us to maintain our operations throughout COVID, a time in which we were ultimately able to complete many projects as school buildings were closed.
Why timber?
Since opening in 2003 we’ve used timber as the primary material in all of our buildings. While reinforcement is occasionally needed for larger rooms, the panels and frames of our schools and sport & leisure buildings are all produced from sustainable wood. When cultivated responsibly, as all of our timber is, it’s one of the few truly renewable materials on the planet, with the strength and durability needed to create permanent structures. Using timber is a crucial part of our net zero strategy, with our design team specifying to meet net zero on every building as standard.
It also looks beautiful and works as part of our commitment to biophilia, blending amazingly into natural environments. Alongside timber, we use a range of other sustainable materials in each building we produce, such as recycled glasswool insulation, and thinner pad-based foundations. We have a range of eco additions like sedum roofs, sun pipes, and HVAC ventilation systems that we also look to include within buildings to bolster their energy performance.
Creating our modular buildings
Thanks to our in-house production facilities, we have complete control over every stage of the creation process. Each building starts with a discussion between the client and our sales team, alongside a survey of their site, after which our architects will work on a bespoke design.
All manufacturing occurs within our facilities, with our team utilising a panelised modular approach, meaning that our buildings are manufactured as a series of flat panels that will be connected together during the installation process. We find that this allows us more flexibility than a volumetric approach, which involves constructing finished modules which are attached to create a finished building at the client’s site.
There are several crucial benefits to all types of offsite modular construction. It allows for a very precise level of adherence to the design created by our team, ensuring swift installation and great building performance. The level of waste created is greatly reduced compared to on-site construction, with simple reuse of materials and recycling of any offcuts. It also offers a significant reduction in on-site time, with quick installation and minimal disturbance.
Want to find out more?
We’ve produced hundreds of buildings over the last 21 years, predominantly within the education industry. Each of our buildings is unique, with a bespoke design built around need, location, and our net zero and biophilic agenda. Whether you want to know more about our manufacturing process or start work on a complimentary design from our in-house architects, speak to a member of our team today.
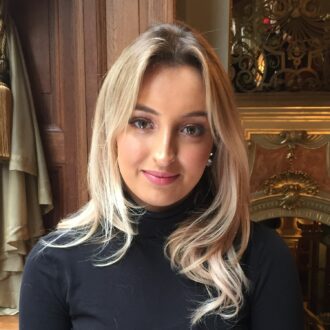
About the author
More posts from our blog
The Benefits of Choosing a Modular Clubhouse Building
A clubhouse needs to serve many functions, from creating social spaces and meeting areas to offering changing rooms and toilet facilities for players. Modular buildings are an ideal solution for creating flexible, purpose-built facilities for sports teams, schools,...
Community Buildings FAQ: Types, Uses, and Funding
Community buildings serve a wide variety of purposes across the UK, often meeting multiple needs at once. From youth centres and village halls to wellbeing hubs and community cafés, these spaces bring people together, support essential services and strengthen local...
Supporting Active School Life With Modular Sports Pavilions
Physical activity is a crucial part of everyday schooling across the UK. But in many settings, ageing facilities and limited space can prevent pupils from getting the full benefit of PE, sport, and outdoor recreation. Modern sports and leisure pavilions offer an...