TG Escapes Blog
What Does Net Zero Look Like in a Modular Building?
Over the last decade, net zero has transitioned from a niche talking point to a critical focus for all construction companies, with clear targets set by the government for the sector. Over the last 21 years, TG Escapes has grown into one of the key modular building providers in the UK, and today we incorporate net zero into our design and build process as standard.
Our experience within the modular sector has made it clear that this approach is the best way to achieve net zero, thanks to a variety of factors including offsite manufacture, material choices, and end-of-life care. While reaching net zero will eventually be a legal necessity, that does not mean it needs to come at the expense of looks, function, and comfort. There are many examples from the modular sector and beyond of brilliant net zero buildings, showcasing the future of construction in the UK and beyond.
Why we need to reach net zero
Over 140 countries, including the UK, USA, and China, have committed to achieving net zero to combat climate change. This means balancing any carbon emissions by absorbing an equivalent amount from the atmosphere. To meet the Paris Agreement’s target of limiting global warming to 1.5°C, global carbon emissions should reach net zero by 2050.
The built environment contributes 39% of global carbon emissions, with embodied emissions from construction materials being a major factor. This existential dilemma for the world requires substantial changes to how we build and support new and existing projects, and commitments from global powers to meet strict targets.
How we define net zero
When considering net zero in a building, modular or otherwise, our team uses two classifications: net zero in operation and net zero in lifetime.
Net zero in operation
To reach net zero in operation, a building’s annual energy use must result in zero or negative carbon emissions. We look to achieve this through a "fabric first" approach that starts with airtight, efficient designs, and includes low-carbon systems like mechanical heat recovery, heat pumps, and solar power for energy generation. At TG Escapes, we achieve this as a standard on all the buildings we design.
Net zero in lifetime
To reach net zero in lifetime, carbon neutrality must be maintained throughout the building’s entire lifespan, from construction to demolition. This includes net zero operation throughout its life and accounts for all embodied carbon. This can be achieved through careful material choice, dedicated end-of-life processes, and offsetting schemes.
What contributes to net zero in a modular building?
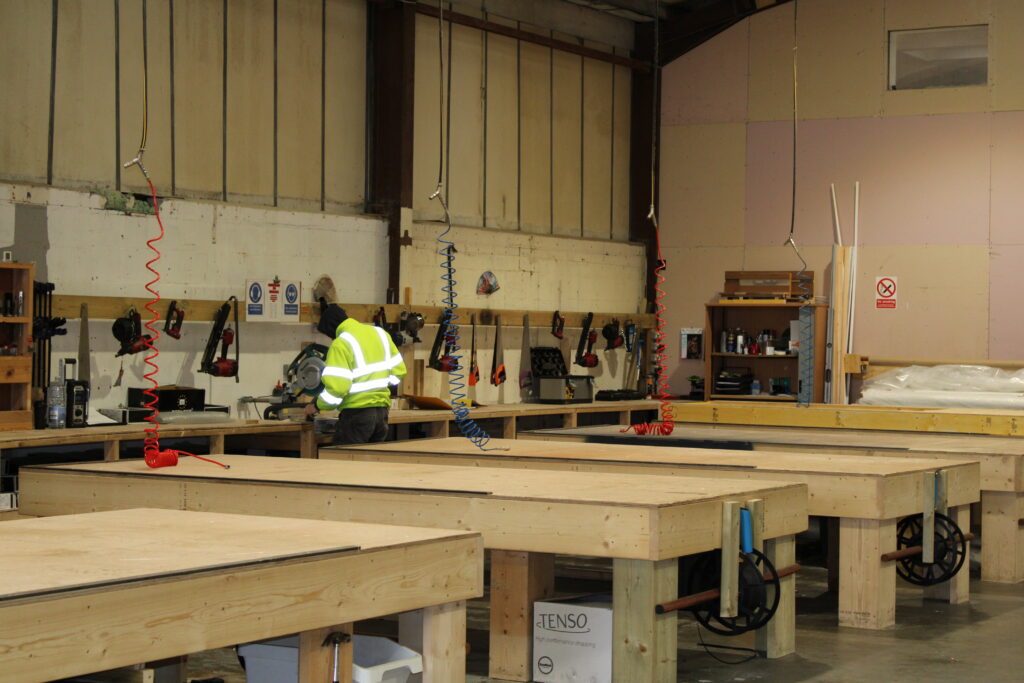
All of our net zero buildings are manufactured by our team
While net zero should be a clear target across all developments, our team believes that modular buildings are uniquely suited to achieving it compared to traditional construction. There are a host of reasons for this, from offsite manufacturing to sustainable material options, and end-of-life dismantling. Alongside these unique benefits, other features including several crucial technological innovations and renewable energy systems can reduce emissions across all buildings. Together, these elements make modular buildings the ideal solution for a sustainable, net zero future.
A careful design process
Creating a building that reaches net zero requires careful planning and a dedicated team initiative at every step. The most cost-effective energy reduction measures occur during the design phase. Integrating passive solar principles, such as building around maximising sunlight to both key rooms and solar panels, can generate more energy and reduce the need for lighting and heating. Using advanced 3D energy simulation tools, designers can model building performance based on variables like orientation, insulation, and airtightness. A meticulous design process ensures that modular buildings maximise energy efficiency and achieve net zero goals.
Offsite manufacture
While modular buildings can be constructed from panels (in our case) or volumetric designs, what makes them unique is their offsite manufacturing process, which greatly reduces carbon output by up to 45%. Constructing in controlled factory environments allows for precise adherence to specifications, reducing material waste and post-build repairs. Modular methods also enable efficient transportation with fewer deliveries, further lowering emissions. Offsite construction also minimises site disturbance, noise pollution, and ecological impact. In terms of long-term sustainability, modular buildings are also easily adaptable, expandable, and repurposable. These advantages make offsite manufacture a key factor in how companies like TG Escapes create net-zero buildings.
Choosing the right materials
The choice of materials is crucial for achieving net zero in modular buildings. Traditional construction often relies on materials like bricks, concrete, and steel, which have high embodied carbon. In contrast, modular designs can utilise more sustainable, low-carbon materials such as timber and recycled insulation, significantly reducing the embodied carbon footprint of buildings. Timber in particular is a renewable material that stores carbon throughout its life cycle, making it an ideal choice for sustainable construction. By prioritising low-carbon materials, modular buildings can better meet net zero targets and set a new standard for environmentally friendly construction.
Utilising modern technology
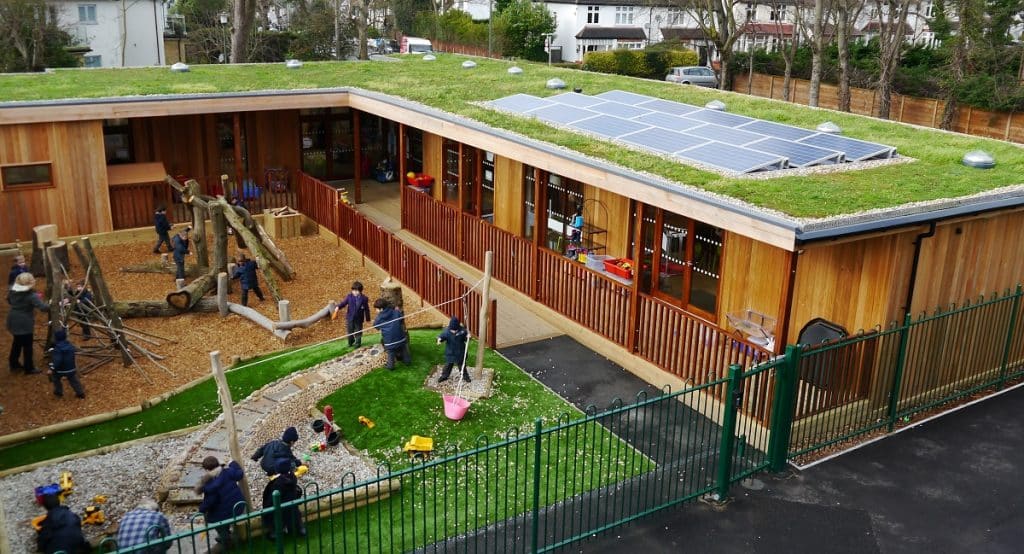
Our nursery for Bickley Park featured both solar panels and a green roof
To achieve net zero in a building most designers would also look to incorporate a range of modern technologies to improve energy efficiency, including:
- Energy generation systems: Integrating renewable energy sources like solar panels and wind turbines will reduce dependence on non-renewable power and lower carbon emissions. These systems generate clean energy on-site, significantly contributing to a building's net zero goals.
- Mechanical Ventilation with Heat Recovery (MVHR) systems: MVHR systems can be installed to maintain excellent indoor air quality while minimising energy use. They recover heat from outgoing air and transfer it to incoming fresh air, reducing the need for additional heating and cooling.
- Light Sensors: Smart light sensors adjust lighting based on occupancy and natural light levels. This technology ensures optimal energy use, reducing waste and enhancing efficiency, with a study showing that they could reduce energy waste by as much as 68%.
- Triple or Quadruple Glazing: Advanced glazing techniques provide superior insulation for buildings, significantly reducing heat loss. This results in lower energy consumption for heating and cooling, contributing to the building’s overall energy efficiency. A study from Glass for Europe showed that swapping all windows for available high-performance glazing options by 2030 could cut annual carbon emissions by 28%.
- Green Roofs: Roofs of buildings not covered by solar panels can be converted into green roofs, covered with grass or other plants, which will act as a carbon sink, further helping a building achieve net zero. Additionally, green roofs can help buildings maintain more consistent temperatures in winter and summer as well as helping achieve a biodiversity net gain.
By incorporating these advanced technologies, our modular buildings can achieve and sustain net zero performance. However, many of these technologies can also be retrofitted to existing buildings to help boost their energy efficiency.
Planning for end of life
When a modular building reaches the end of its life, several strategies can ensure it contributes to net zero goals, achieving net zero in lifetime. The UK Green Building Council recommends that existing buildings be retained for reuse, new buildings be designed for repurpose or disassembly, waste materials from demolished buildings be diverted from landfills, and energy-efficient demolition equipment be used.
Choosing materials like timber offers clear end-of-life solutions. Timber can be repurposed or recycled, minimising waste and reducing the carbon footprint. Modular buildings designed for easy disassembly allow components to be reused, further contributing to sustainability. This approach not only supports a circular economy but also ensures that the environmental impact of construction is minimised throughout the building’s lifecycle.
Careful use of offsetting schemes
While carbon offsetting can help achieve net zero buildings, many experts have expressed concerns about relying on it. When buildings cannot generate all their own energy and must draw from the grid, carbon offsetting can be used to balance the emissions. Similarly, offsetting can be used to address embodied carbon emissions from construction to verify a building as net zero carbon.
However, relying solely on offsetting doesn't reduce fossil fuel consumption, which is crucial for addressing climate change. The Commission on Climate Change (CCC) suggests that most sectors, including buildings, need to reduce emissions close to zero without offsetting.
Some of our favourite net zero projects
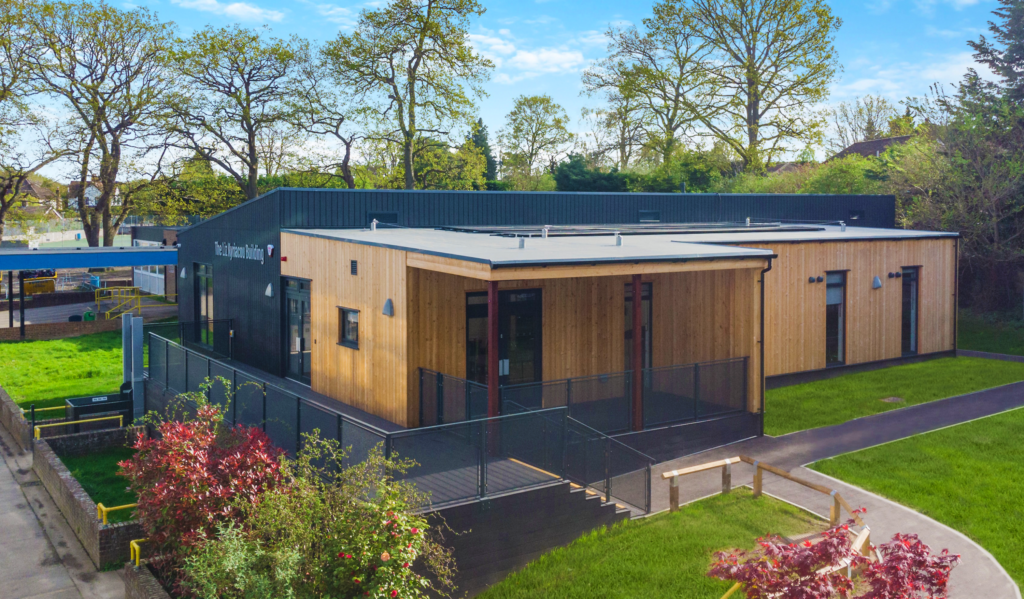
Our recent net zero project at Woking High School
TG Escapes had long championed timber and other sustainable elements within our buildings, before completing our first A+ energy-rated building in 2020. Now, we specify every building we design and build to reach net zero in operation as standard (and can meet net zero in lifetime if desired).
By completing all work in-house, including our bespoke designs, the construction of our modular panels, and all installation work, we can ensure that sustainability goals are met throughout. Here are three of our favourite net zero projects that we’ve completed for schools across the UK.
- SEND Hub at Woking High School: In collaboration with Surrey County Council, we recently completed a fully net zero building for visually impaired students at Woking High School. Featuring innovative screw-piled foundations, the building includes three classrooms, breakout spaces, offices, and toilets, all designed to meet the specialist needs of their students. This project overcame challenging site conditions and was completed in 22 weeks, upping the school's capacity while providing a sustainable learning environment.
- Net Zero Block at Brune Park: Completed in 2023, our team were especially proud of this timber frame building for Brune Park Community School. Replacing an old SCOLA building, the new structure includes nine classrooms, breakout spaces, offices, and a large atrium. It provides flexible classroom space and conferencing facilities, meaning it can also act as a business hub. We were thrilled to achieve an A+ EPC rating.
- Multi-Classroom Block at Samuel Ryder Academy: Completed in 2020, this net zero multi-classroom block at Samuel Ryder Academy was our first A+ rated building. Featuring specialist heating, ventilation, lighting, and solar power systems, it also boasted a custom exterior finish to blend seamlessly with existing structures.
Want to find out more?
TG Escapes works on net zero modular buildings for clients across the UK, with a focus on the education sector. Each of our projects starts with a complementary design process, with our in-house architects working with clients on a bespoke blueprint, which will be presented with a fully costed price for manufacture and installation. Explore our case studies, or speak to a member of our team to find out more about how we can achieve net zero in your next project.
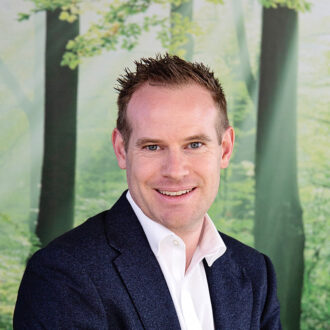
About the author
More posts from our blog
Supporting Active School Life With Modular Sports Pavilions
Physical activity is a crucial part of everyday schooling across the UK. But in many settings, ageing facilities and limited space can prevent pupils from getting the full benefit of PE, sport, and outdoor recreation. Modern sports and leisure pavilions offer an...
Creating Calm, Purposeful Spaces for SEMH Learners
For students with Social, Emotional, and Mental Health (SEMH) needs, the right environment can make a world of difference. In an ideal setting, buildings are a key part of the therapeutic process, shaping behaviour, supporting emotional regulation, and helping...
How Modular Changing Rooms Can Transform Your Facility
Over the years, we’ve helped schools, councils, and commercial clients develop purpose-built changing facilities that are attractive, robust, and tailored to their needs. With a streamlined design and build process, we create high-quality bespoke solutions ideal for a...